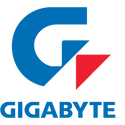
Production Gigabyte G1.Sniper 2 Features PCI-Express Gen. 3
About a month ago, we were treated to the first pictures of G1.Sniper 2, Gigabyte's first LGA1155 motherboard in its G1.Killer series of motherboards targeting the gamer-overclocker market segment. High resolution pictures showed the prototype of having PCI-Express Gen. 2 slots like most other LGA1155 boards. It turns out, according to a photo-session of a production sample by tech-blog SIN's Hardware, that Gigabyte refined the design with the production version (the one that will be sold in the markets), it features PCI-Express 3.0 (Gen. 3) graphics slots.
For a LGA1155 motherboard to have Gen. 3 PEG slots, it requires Gen. 3 specifications compliant switching circuitry, which wasn't available to motherboard vendors when they were designing their first LGA1155 boards. With availability of those components, motherboard vendors are not wasting any time in rolling out new variants of their LGA1155 boards that feature Gen. 3 PCI-Express slots. Gigabyte placed "PCI-Express 3.0" marking on the board manually using stickers, going on to show that adding Gen. 3 slots indeed may have been a last-minute decision at Gigabyte. The other interesting marking on the G1.Sniper 2 carton is the mention of the board being ready for upcoming 22 nm "Ivy Bridge" Core processors. More pictures, and a preview at the source.
For a LGA1155 motherboard to have Gen. 3 PEG slots, it requires Gen. 3 specifications compliant switching circuitry, which wasn't available to motherboard vendors when they were designing their first LGA1155 boards. With availability of those components, motherboard vendors are not wasting any time in rolling out new variants of their LGA1155 boards that feature Gen. 3 PCI-Express slots. Gigabyte placed "PCI-Express 3.0" marking on the board manually using stickers, going on to show that adding Gen. 3 slots indeed may have been a last-minute decision at Gigabyte. The other interesting marking on the G1.Sniper 2 carton is the mention of the board being ready for upcoming 22 nm "Ivy Bridge" Core processors. More pictures, and a preview at the source.