|
Laing
DDC 3.2 (MCP 355) Pump Top Test Comparison - 11 Tops Tested!
Introduction
Welcome to my multiple pump top
and reservoir top
shootout. Over time
I’ve acquired the
necessary tools and techniques needed to fully test pumps. The
DDC 3.2 is Laing’s newest revision of the extremely popular
DDC pump, also
rebranded as the Swiftech MPC355.
This
pump comes with a stock top that is designed with
3/8” fittings and the inlet
barb has a sharp very small diameter 90 degree bend.
Overall
the pump’s design is really ideally configured in power and
pressure
orientation for today’s water cooling systems. It’s
almost the perfect water cooling pump, good power/heat dump ratio, good
pressure capabilities, nice compact size.
Unfortunately the stock top only comes with
3/8” barb fittings and that
sharp 90 degree inlet bend looses a fair amount of efficiency.
Along comes the aftermarket
tops.....straightening out that inlet and providing the much more
desireable G1/4 fitted barb. Unfortunately
there is not alot of performance related data on the existing tops.
I'm a bit of a measurebater and like to know which performs
better, and since I have the
tools to test them, I figured, why not?
I’ll
ask around and gather up as many as I can and test them all on the
same pump and give the community some real comparative data.
My
ultimate hope is that this will encourage a few tweaks and we'll even
have better tops to choose from later...win win!!
Testing Sponsors
First I wanted to
give a special
thanks to those people who really made this test availailable.
The following folks are truely committed to providing the
water
cooling community better information and they provided me either loaner
samples to test and return or product samples I can keep(I'm all for
more water cooling goods!):
 Coolmiester (XS
member name) of Coolercases UK
- Please visit their website and forums. They provide a great
resource to the community and wide range of products.
Coolmiester
sent me the following loaner samples: Petra's DDCT-01s Top, EK-DDC X-Top G1/4, EK-DDC X-Top G3/8, Alphacool DDC plexitop, and the Alphacool DDC Plexi Reservoir.
Five of the testing tops, thanks a bunch, very much
appreciated!
 Petra of Petra's
Tech Shop
- Provided me with a loaner sample of the Koolance DDC top.
Since
I already had a a DDCT-01s top, they offered and sent me the Koolance
top they had from thier own testing. Petra's Tech shop is my #1 pick
for shopping in the USA, they are like the newegg of water cooling for
us USA folks, only 10X the customer service. I particularly
encourage you to shop there, because they are also truely committed to
testing and finding out the truth about water cooling products.
That means worlds to me and I order stuff from them all the
time.
How many Petra pens do YOU have?...:)
 Paul from XSPC
provided me with both the XSPC Laing DDC top and their newly
release XSPC Acrylic Reservoir DDC Top
product samples. A UK based company with some very refined
performance products.
 Jeremy from Danger Den provided me with
a sample their Danger Den DDC acrylic top.
Danger Den is another great manufacturer and reseller of all type of
water cooling products, based here in my home state of Oregon in the
USA. As you'll see in many of my other reviews they are very
committed to producing products with good flow rate capabilities.
I've really enjoyed reviewing many of Danger Den's products,
they
are great folks that manufacture great products!!
 Gary from Sidewinder Computer Systems
provided me with an OClabs sample. I shop at Sidewinder very
regularly and highly recommend you check them out. Sidewinder is
also committed to providing various forum members gear to test, and
very committed to supporting forum members in their testing adventures.
They carry a wide range of water cooling gear at the very best prices!
 Rob
from the Watercoolingshop.com provided me with the EKG3/8" Barbs for
the EKG3/8" X-Top. He also provided these nice G3/8" to G1/4"
adapters which I used in some recent radiator testing. They have
a wide variety of water cooling gear and specialize in water cooling
parts. I highly recommend them!
NaeKuh (XS member) |
Another
very active member in the water cooling comminuty always out to try new
things. I've been building him a TEC chiller and while I was
at
it he sent me his EK X-Res 140.
Unfortunately I sent this sample back to him before I retested
all the samples measuring total head, so I do not have that result. |
Thanks....you all made this possible!!
The
Pump Used for Testing - Swiftech MPC 355 (18watt), or Laing DDC 3.2
The pump I used in all of this testing is one that I recently purchased at Petra's,
it is the newest iteration of this popular little hard working pump.
Very possibly the most popular pump out there for water
cooling.
So $75 bucks later along with Petra's amazing customer
service, I
had a happy little pump sitting on my test bench. I happened
to
be a long time Swiftech MPC655 (Laing D5) vario user, so it was fun
trying out this new little pump. The older and more powerful
DDC2 is no longer in production, while performing better it also had
some proplems with pump failure. So far this new DDC 3.2 pump
appears to be doing much better, I havn't heard very many problems with
it, and it appears to be a completely redesigned pump.
Anyhow,
I'm not here to talk about the pump specs, there's plenty of that
available on the internet, but I've linked you to some good articles
down below here. It's a very good and popular pump.
Swiftech's website on the MPC355 -
They rebrand this pump and include their own accesory package.
Laing's website for the Laing DDC3.2
- They manufacture this pump. DDC3.2 brochure.
One little bit I would like to add before I go on to the tops is a
little testing I did with the stock pump to explore over/undervolting
potential. In the end I found that you get some decent gains
from overvolting and you can really turn the pump down ALOT
undervolting. Unfortunately it's a little scary because
exceeding some very defined limits will not allow the pump to start.
It appears there is some sort of protective circuitry built
into the pump to prevent you from overvolting the pump very much.
I found that limit to be around 12.95 to 13.00 Volts and it
was a limit on startup only. I could start the pump at 12.00V
and turn voltage up to 13.5V, but after turning off my PSU and trying
to start it at 13.00 more, it simply would not start. This
could be a very bad situation if you were overvolting to 12.9V and just
happend to have a surge of power that resulted in your pump not
starting because your PSU surged and produced 13.0V!... Up to you if
you want to overvolt, but it definately has some risk (possible failure
to start and overheating). I'm not very experienced in ATX
power supply specifications, but I know my current PSU(OCZ GameExtreme
700) actually produces around 12.4V on average, so the 12.9V limit is
probably designed to give just enough room for differences in
your average power supply, very little extra. Not sure it
would be worth the extra .1GPM, and if you wanted to undervolt you
could modify the DDC3.2 to be a DDC 3.1 by removing the soldered
bridge. DDC3.2 VS DDC3.1 Photo Difference
So you'll get about .1GPM gain with the extra overvolting, 10V runs
pretty close to a DDC3.1, and 7V is really weak and nearly useless. In
the end I don't think it's worth messing with, I'd suggest running it
at 12V for maximum performance or mod it down to a 3.1 for complete
silence, then you don't need to worry about any special power supply
and exceeding the limits of voltage operation.
Performance
Measurements
P/Q (Pressure Vs.
Flow Rate Curves)
First and probably the most
important is the ability to
measure a pump’s PQ curve.
You’ve
probably read in your own pump specs two general numbers
that are
specified. One is
typically the maximum
head or lift. The
second is the maximum
flow rate. These
two numbers are two
points that are part of this curve.
PQ
stands for P being pressure and Q being flow rate, so in the end
it’s just a
curve that represents the relationship of pressure and flow rate.
Unfortunately these two numbers
or points on the curve only
indicate points of value where our pumps never operate under a real
water
cooling system. Maximum
flow only occurs
when there is absolutely no resistance.
And maximum pressure only occurs when
you’ve completely stopped the flow
(pinch and kink your tubing, now you have max pressure, but zero flow). Furthermore
they do not provide you with
information about the curve or path in between these two points (The
results will show you how important curve "shape" is as indicated by
the DD top". There
are all types and shapes of this curve
and it’s critical to plot the entire curve and particularly
look at the range
between 1 GPM and 2.5 GPM because this range is where the system
pressure drop
curves typically intersects the pump curve.
Where these two curves intersect is what determines
your water cooling
system flow rate. So
pressure vs. flow rate is
“The” ideal measurement of pump performance that
determines flow rate. After
collecting this data, I’ll evaluate
these curves where it is important and explain what they mean in more
detail.
Update 4-5-08 Total Dyamic Head (Outlet - Inlet) Water Pressure Measured
In the past
all of the pump testing I have seen in watercooling has generally only
measured the outlet nozzle of the pump (Outlet/Discharge Head Pressure), 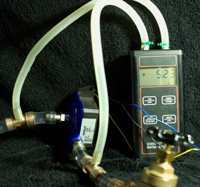
however after running this series of tests I became increasingly
interested in why some of the reservoir tops had a performance
advantage. After further research I discovered that to capture
the full power of a pump, it's important to measure pressures as the
suction side of the pump (Inlet/Suction Head Pressure). In the
end, the energy provided by the pump comes in two primary forms,
pressure differential and flow rate. To measure pressure
differential or Total Dynamic Head of a pump you take the outlet
pressure and subtract the inlet pressure. A dual input manometer
which I use is ideal for this testing as I can simply install a
pressure sensor Tee fitting at both sides of the pump and read a direct
pressure gain across this pump. The relative comparison between
the tops is very similar in my net end result, but the overall power
improvement will make some difference in flow rate calculations and in
the end it's also the proper way to test pressure on a pump. So
from this point forward, I will be testing pumps and measuring "Total
Head" instead of just "Outlet/'Discharge Head".
Power Consumption vs.
Flow Rate
In addition to measuring
pressure and flow rate, I also
collected the pump power draw in terms of voltage and current (amps). Voltage was necessary to
ensure a proper
12.0V being fed to the pump anyhow, and it’s very easy to add
another multi-meter
in to measure current. This
provided me with
the ability to measure how many watts were being drawn by the pump at
each test
point. This information is not
particularly important in comparing tops using
the same pump motor, but it is EXTREMELY important in pump selection
because a
large percentage 60-90% of the pump power consumption is dumped into
the water
cooling loop as HEAT! The added benefit of collecting this
information is explained later with efficiency comparisons.
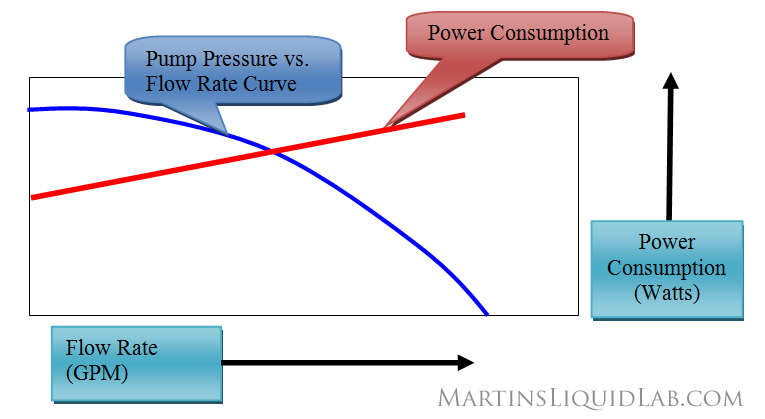
Efficiency (Updated 4-5-08)
In addition to providing the
two above performance measures,
I also wanted to provide some sort of means to measure efficiency.
This is a measurement of water horsepower to break horsepower and
simply shows you where the pump and top combination peaks in
efficiency. Smaller pumps generally have lower efficiencies, but
this does at least provide you with how efficient each top is and where
they peak in flow rate. On pump selection ideally you would
select a pump that peaks in efficiency where your system flow rate
resides, but that's more of a criteria engineers use when selecting
large pumps. What I did find interesting is that many of the pump
tops peaked in efficiency at flow rates higher than typical.
The
DDC 3.2 Pump Top Contenders
The following alphabetical list of pump tops were included for testing:
Alphacool DDC plexitop
Alphacool DDC Plexi Reservoir
Danger Den DDC acrylic top
EK-DDC X-Top G1/4
EK-DDC X-Top G3/8
Koolance COV-PMP01P
OClabs XP-Top
Petra'sTech DDCT-01s Acetal Top
XSPC
Laing DDC top
XSPC
Acrylic Reservoir DDC Top
Stock
DDC3.2 or MPC355 Pump with stock top
Testing
Equipment and Methods
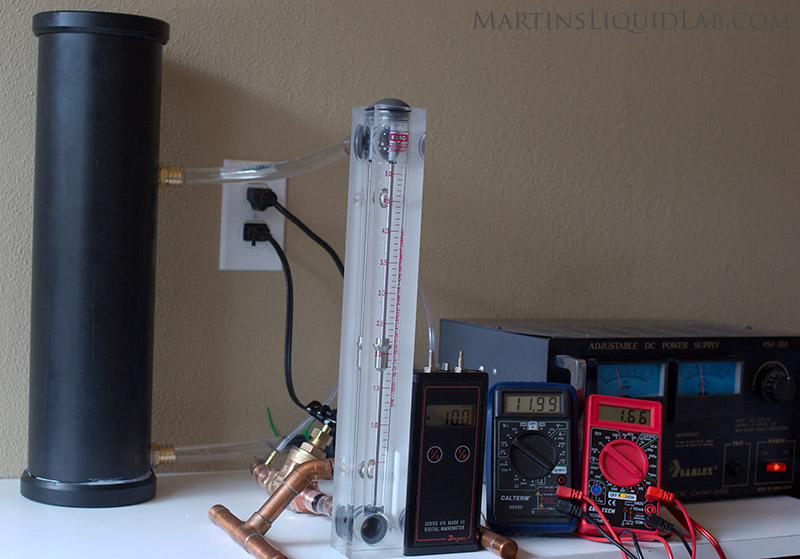
Note the above photo is the old test method of outlet discharge
pressure only, all tests have been redone to include Inlet pressures.
Pressure
– Dwyer Series 475 Mark III digital manometer.
– Measures differential pressure, calibrated zero in setup at
zero flow rate. Note
this corrects out
Atmospheric pressure (not PSIG), and it also corrects out static
pressure from
the test loop. In
the end this is a true
measurement of pressure added by the pump with atmospheric and static
pressure
errors removed. Accuracy
.5% of FS or 1”
H20 per manufactures specs. In
testing,
the actual pressure fluctuates typically 3-4” H20 at high
pressure down to
about 1” H20 at lower pressures.
In the
end, I would estimate overall operating pressure to be accurate to
about 1. to
.2psi
Flow
Rate – King Instruments 0 - 5 GPM, 250mm scale 7520
series flowmeter. – Accurate to 2% of FS, so about
.1GPM per the
manufactures specs
Voltage
and Current
– Standard multimeters were used, one was connected in
parallel for measuring
voltage, and one in series on the power line to measure current. These are not scientific
grade meters, but accurate
enough for these purposes. Comparing several multimeters, voltage
between them was accurate to within about .05V.
DC
Power – Samlex DCvariable
power supply, 5AM max and 0-30V infinitely variable. I
continuously monitored and recorded actual voltage from a separate
multimeter and adjusted voltage to be within .03V of 12.00V.
Variable Flow
Resistance 3/4" Brass Valve – In order to vary the
amount of flow rate precisely, I chose to
use a ¾” brass screw type gate valve with custom
fabricated 5/8” copper
barbs. A standard
½” globe valve is
lower restriction, but it did not provide a very precise or fine means
of
adjustment. The
larger gate valve is also
low restriction and provides much finer control over the restriction
for more
precise control. In
the end this valve
provides the needed variable resistance to adjust restriction and
control the
flow rate. Close
the valve all the way
down and you have maximum pressure.
Open
the valve a little until you have .5GPM and I can record the pressure
and power
consumption at that point. Open
a little
more to .75GPM and I’m ready for the next data point and so
on.
Custom
4" x 24" reservoir – Because
it was extremely important to quickly remove any air bubbles in the
system I have, I fabricated my second iteration of a test reservoir.
The large cross sectional area allows the velocities downward
to
be extremely low allowing air to work it's way out almost instantly.
In addition I machined a large taper and radius on the 1/2"
NPT x
5/8" brass barbs used to minimize entrance losses from the reservoir to
the pump feed tube.
10 minute bleed and warm up
– I allowed
each pump to bleed 10 minutes and adjusted the flow rate up and down
to completely purge the system of air before testing commenced.
The large reservoir typically would bleed the pump silent of
air
within 1-2 minutes, but I left it on for the full 10 just to make sure.
.25 GPM record
interval - I recorded data starting at .5GPM in .25GPM
increments until the pump maxed out flow rates and my gate valve was
completely
open.
Test Fluid is
Plain Cold Tapwater
- Standard cold tapwater was used for all testing. In between
test runs, the system was drained and cold tapwater was used to refill
the system. Our household water is clean treated drinkable
and the specific
gravity
very close to 1.0 and viscosity of negligible difference. Someone may
wonder why I didn't use distilled water, and I
could
have, but considering a water cooling system is typically going to have
ethelene glycol or some other coolant mixture of addatives, I figured
the very minor amounts of chlorine added to our drinking water is
insignificant in comparison. Besides this is a relative
comparison and all tops are tested with the same fluid so any error
would be reflected the same in all tests.
Top Mounting
- All tops
were mounted with the same amount of torque and pressure which is a
fairly snug fit. But before doing so I carefully inspected
the
alignment of the top to the alignment of the impeller inlet.
The DDC tops were all capable of shifting around 1-2mm, and I felt it
was important to get a perfectly centered inlet for each test.
Pressure
Vs. Flow Rate Curve Comparison
First up is the entire curve, and the area to note is in between the
two red system curves. The left most limit would be an
extremely
high restrictive system and to the right would be an extremely low
restrictive system.
The XSPC reservoir top is KING of
the DDC 3.2 tops tested!
It
should be noted that on average and low restriction
systems, all
of the tops tested do provide you a fairly significant gain in flow
rate performance over the stock top.
Estimated Flow Rates
If the above curves are difficult to understand, I've extracted the
following flow rates for a relatively high restriction system, average restriction system, and low restriction system:
High Restriction System = Fuzion w 4.5mm Nozzle, Fuzion GFX, HWLabs 480GTX, Reservoir, 7' 7/16" ID Tubing
Average Restriction System = Swiftech Apogee, Swiftech MCW-60, Hwlabs BIX 360, 5/8" Tee, 7' 7/16" Tubing
Low Restriction System = Danger Den MC-TDX, PA160, 5/8" Tee Line, 7' 7/16" Tubing
Side Inlet Performance
I did experiment with side inlet
performance with my initial discharge only pressure testing and found
that performance suffered significantly to the point where the stock
top performs better in many cases. I didn't retest these side
inlets in measuring total head, so I have pulled those results, but I
expect them to scale similarly and the stock top performs nearly as
well as any of the aftermarket side inlet tops. There is a significant
loss in the 90 degree bend.
I would not recommend using the side inlets unless you absolutely have to.
Conclusion
I think it's pretty
amazing that
these pump tops can gain so much efficiency over the stock pump top,
but they are. Kudos for doing a great job there!!
The XSPC tops are performing the best in all system configurations, a
true tribute to the design and tweaks that have occured in the current
design...excellent!!
The remaining tops all perform very well and have trade offs between
each other depending on the system restriction. Some are
slightly
more tuned lower flow rates and others for higher flow rates.
In the end, these tops can afford you as much as 1.08 GPM gain on low
restriction systems, .51 GPM on an average restriction system, and .12 GPM
on extremely high restriction systems..... that's a good flow rate gain!!
Possible
Design Tweaks
With that general trend for more restriction and nozzles, I would
encourage any tweaks to these already suberb designs to give a little
on the flow rate side and tune these pump tops for more pressure.
The engineer in me can't help but think there is still a way
to
make something already great even better..:) I think some of the tops
could be improved by tweaks in the following:
- Utilize a true "Spiral" shaped volute - this is a
little
more complicated to design, but it only up front tool path
design costs with CNC. A circular volute is
not
the optimal shape to release flow around the perimeter of the impeller.
Water is incompressible (for all practical purposes), so a spiral
design with an ever changing radius to provide space for the impeller
water coming off is the most efficient shape and allows the entire
impeller to do work rather than primarily one side. The semi
spiral and relief cut to simulate a true spiral
curve do not appear to be nearly as efficient as the full spiral.
It actually appears that a regular circular volute shape is doing
better than those with relief cuts or two simple curves to simulate a
spiral..
- Smaller Inlet Nozzle - I understand the manufacturing
simplicity in using a 11.8mm drill bit to drill and then fully tap the
inlet hole, but the size exceeds that of the impeller inlet hole, so
all you do is introduce yet another sharp entrance loss and this is
significant in the pump design.
- Smaller Outlet Nozzle - It appears the nozzle size
really
is optimally matching that of the impeller and going larger on the
outlet port only help flow and going too big may hurt pressure.
- Experiment with tapered and protruding inlets - This
is
just a theory of mine, but I think something besides a straight tube
inlet is beneficial as the water has to turn 90 degrees after entering
the impeller. If the jetstream of water is slightly moving
towards the perimeter as it enters the impeller, I think that helps
reduce that entrance loss. A protruding inlet will also
better
seal the volute chamber from the inlet....you would just have to
experiement and ensure impact is not possible which is difficult with
the play possible in all but the stock top (which has cast alignment
pins that accept the bolts and).
- Consider using a ball end endmill for the final
perimeter
cut of the volute. Another theory of mine, but I think if the
perimeter catching the water was radius and had a nice smooth spiral
transition into the outlet port, you would gain even more efficiency.
The cross sectional shape of a circle or pipe is the most
efficient shape (least amount of frictional surface area). It
appears that very small "details" are key in pump top design, so this
may be another detail that returns with performance.
- Consider using recieving studs that extend from the
pump
top like the stock top. This ensures the top is perfectly
aligned
with the impeller inlet and eliminates installation errors that can
cause imperller to top impact and damage to the pump.
- Smooth finish - roughness coefficients can steal away alot
of energy, and nice glass like smooth finish in the perimeter of the
pump top and smooth transitions throughout can only be of benefit.
If you have any
additional tops to test or corrections in this collection of results
please let me know.
Thanks!
Martin
|