- Joined
- Oct 9, 2007
- Messages
- 47,852 (7.39/day)
- Location
- Dublin, Ireland
System Name | RBMK-1000 |
---|---|
Processor | AMD Ryzen 7 5700G |
Motherboard | Gigabyte B550 AORUS Elite V2 |
Cooling | DeepCool Gammax L240 V2 |
Memory | 2x 16GB DDR4-3200 |
Video Card(s) | Galax RTX 4070 Ti EX |
Storage | Samsung 990 1TB |
Display(s) | BenQ 1440p 60 Hz 27-inch |
Case | Corsair Carbide 100R |
Audio Device(s) | ASUS SupremeFX S1220A |
Power Supply | Cooler Master MWE Gold 650W |
Mouse | ASUS ROG Strix Impact |
Keyboard | Gamdias Hermes E2 |
Software | Windows 11 Pro |
Andreas Schilling with Hardwareluxx.de, as part of the Intel Tech Tour Israel, got to hold a 12-inch wafer full of "Raptor Lake-S" dies. These are dies in their full 8P+16E configuration. The die is estimated to measure 257 mm² in area. We count 231 full dies on this wafer. Intel is building "Raptor Lake" on the same 10 nm Enhanced SuperFin (aka Intel 7) node as "Alder Lake." The die is about 23% larger than "Alder Lake" on account of two additional E-core clusters, possibly larger P-cores, and larger L2 caches for both the P-core and E-core clusters. "Raptor Lake" gains significance as it will be the last client processor from Intel to be built on a monolithic die of a uniform silicon fabrication node. Future generations are expected to take the chiplets route, realizing the company's IDM 2.0 product development strategy.

View at TechPowerUp Main Site | Source
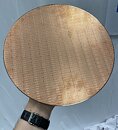

View at TechPowerUp Main Site | Source