PWM Controller - Isolator
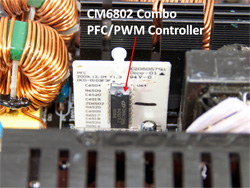
The main purpose of the PWM controller is to maintain a regulated output voltage and control the amount of energy being delivered to the load (system). The aforementioned are accomplished by adjusting the duty cycle of the main switches. The duty cycle can be adjusted from 0 to 100 percent but usually its range is smaller. With great approximation we could say that output voltage is the product of input voltage and duty cycle (Vout = Vin × duty cycle).
The PWM controller uses a voltage reference as the PSUs “ideal” reference to which the output voltage is constantly compared. In the PWM IC there is a voltage error amplifier that performs a high gain voltage comparison between the output voltage and the above-mentioned reference. According to this comparison an error voltage-to-pulse width converter sets the duty cycle in response to the level of the error voltage from the voltage error amplifier. Besides determining the duty cycle of the main switches the PWM controllers usually incorporate and other functionalities, as soft-start circuit which starts the PSU smoothly reducing large inrush currents, over-current amplifier that protects the PSU from overloading, undervoltage lockout that prevents the PSU starting when the voltage within the control IC is too small to drive the main switches etc.
In order for the voltage feedback, from the DC outputs, to reach the voltage error amplifier of the PWM IC an isolated feedback is needed. There are two methods of electrical isolation, optical (optoisolator) and magnetic (transformer). In modern PSUs optoisolators are commonly used. The voltage error amplifier is placed on the secondary side of the optoisolator.