Friday, February 16th 2018
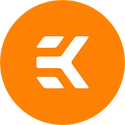
EK Announces Monoblock for GIGABYTE X399 Motherboards
EK Water Blocks, the Slovenia-based premium computer liquid cooling gear manufacturer is releasing a new Socket TR4 based monoblock made for several GIGABYTE X399 motherboards. The EK-FB GA X399 GAMING RGB Monoblock has an integrated 3-pin RGB Digital LED strip which makes it compatible with GIGABYTE Fusion, thus offering a full lighting customization experience.
This is a complete all-in-one (CPU and motherboard) liquid cooling solution for two GIGABYTE AMD X399 Chipset based motherboards that support AMD Socket TR4 AMD Ryzen Threadripper processors. This monoblock is compatible with the following GIGABYTE motherboards:
This X399 platform based monoblock features a redesigned cold plate with a fin area that covers most of the Ryzen Threadripper IHS surface. The design also ensures that the monoblock cold plate is covering the entire Ryzen Threadripper processor IHS, thus enabling better thermal transfer. The base of the monoblock is made of nickel-plated electrolytic copper while the top is made of quality acrylic glass material. The main nickel plated mounting screws and brass screw-in standoffs are pre-installed so that the installation process is quick and easy.
The monoblock is equipped with a Digital RGB LED strip that connects to the dedicated 3-pin digital LED header. GIGABYTE AORUS X399 series motherboards boast the most advanced LED system in the market today and with the GIGABYTE RGB Fusion App, users can individually address color to each LED on the monoblocks integrated Digital LED strip. The LED strip cover can easily be removed for adjusting the cable orientation or replacing the Digital LED strip with an ordinary LED strip or any other custom solution as well! Another, standard 4-pin 12V RGB LED strip is included in the box that can connect to the motherboard's 4-pin LED header or it can be connected to any other standard 12V 4-pin LED controller.
EK-FB GA X399 GAMING RGB Monoblock is made in Slovenia, and it is available for purchase through EK Webshop and Partner Reseller Network, priced at 125.95€ (incl. VAT).
This is a complete all-in-one (CPU and motherboard) liquid cooling solution for two GIGABYTE AMD X399 Chipset based motherboards that support AMD Socket TR4 AMD Ryzen Threadripper processors. This monoblock is compatible with the following GIGABYTE motherboards:
- GIGABYTE X399 Aorus Gaming 7 (rev.1.0)
- GIGABYTE X399 Designare EX (rev.1.0)
This X399 platform based monoblock features a redesigned cold plate with a fin area that covers most of the Ryzen Threadripper IHS surface. The design also ensures that the monoblock cold plate is covering the entire Ryzen Threadripper processor IHS, thus enabling better thermal transfer. The base of the monoblock is made of nickel-plated electrolytic copper while the top is made of quality acrylic glass material. The main nickel plated mounting screws and brass screw-in standoffs are pre-installed so that the installation process is quick and easy.
The monoblock is equipped with a Digital RGB LED strip that connects to the dedicated 3-pin digital LED header. GIGABYTE AORUS X399 series motherboards boast the most advanced LED system in the market today and with the GIGABYTE RGB Fusion App, users can individually address color to each LED on the monoblocks integrated Digital LED strip. The LED strip cover can easily be removed for adjusting the cable orientation or replacing the Digital LED strip with an ordinary LED strip or any other custom solution as well! Another, standard 4-pin 12V RGB LED strip is included in the box that can connect to the motherboard's 4-pin LED header or it can be connected to any other standard 12V 4-pin LED controller.
EK-FB GA X399 GAMING RGB Monoblock is made in Slovenia, and it is available for purchase through EK Webshop and Partner Reseller Network, priced at 125.95€ (incl. VAT).
3 Comments on EK Announces Monoblock for GIGABYTE X399 Motherboards
I've always thought PC watercooling products were unjustly and exorbitantly priced. I used to work with and in Industrial fittings for foodsafe applications and many of those fittings have the same exact types of designs like British standard pipe parallel threads [BSPP or what is PC enthusiasts will recognized as G1/4" thread] and compression connections, though they were always made with more robust materials and designs. By "work" with, I mean I was the head Director of Inventory and Procurement for a large, national service company that would service commercial food equipment (among other types of equipment) for clients like Starbucks, Target, Regal Cinemas, etc. So I had to procure the most reliable and cost effective fittings available. Eventually I became intimately knowledgeable on all their aspects even including knowing the exact composition of the alloys used to manufacture them, the exact process they used for electro plating whether it was nickel or something else as well as the thickness of those layers. Eventually, like with all inside sales, you become friendly with the employees of other companies and since they trust you, they start letting you in on some "secrets". Basically, I came to know various manufacturers of all sizes and what the costs of production truly are for these fittings. Now, even if a company, like EK does its machining "in house" (e.g. using their own facilities and CNC equipment to produce waterblocks), they're most likely still purchasing their fittings from some manufacturer since fittings, although they may require machining at certain points, cannot be produced entirely from machining, they're either mold/form cast, thermally extruded also known as hot forming, or variations/combinations of these processes...bottom line, I'm almost certain EK (or any other PC watercooling company) does not have the volume necessary to justify their own in house production, which means they buy them from much larger manufacturers who do have the volume necessary, and that keeps costs low.
The fittings I dealt with mostly were either 304 or 316 stainless steel and usually came with compression tube, threaded, and/or John Guest connections, though there were plenty of brass/nickel plated (especially valve block assemblies) fittings as well. [FYI, a "John Guest" fitting is what people typically call a "push-in" fitting, John Guest is the british man that created them). Interestingly, although raw Brass costs more per unit of measurement than 304 or 316 SS, due to certain particular factors in the production processes, the net cost of stainless steel fittings is actually higher than nickel plated brass. Although there are many reasons for this, they include the fact that SS is harder requiring more time for production, requires much higher heat and therefore more energy for thermal forming, more expensive dies, cutting and forming equipment as well as shorter lifespan for working with SS, and importantly, when compared to brass, copper, and even aluminum, SS scrap is for all intents and purposes worthless, and cannot be used on the backend to lower net production costs. That being said, when producing a 316 SS fitting with the same BSPP threads found on PC fittings, Viton-B O-rings (probably better than on PC fittings), and much, much greater wall thickness to accept much higher pressures, I was told by someone on the inside at one of these manufacturers that they sell them to their customers at somewhere between 50%-90% of what the final consumer's price SHOULD be, and then proceeded to provide me a few precise figures. Based on that, and extensive research into brass production, I'd feel confident saying that EK is probably paying approximately between $0.50 to $2.50 for your typical nickel-plated brass compression fitting with a 1/4" BSPP thread and a 16mm tube connection. This cost will vary based on the volume of their orders, but I would think it impossible for them to be paying anywhere above $2.50 each, with that figure even being an unlikely upper limit.
Considering that I could, at this very moment, purchase a 316 SS 1/4" BSPP x 16mm female tube at $5.00-$7.50 or less for a quantity of one as a normal consumer and considering that 316 SS fittings cost more to produce (and since they can handle pressures upwards of 3000 PSI and thus are much thicker equaling more material), this estimate seems reasonable. It's interesting to note that the ONLY difference between an "industrial" compression fitting and a PC one (despite the industrial fittings usually having thincker better materials), is that the industrial fitting will come with wrench flats, which is nothing more than an aesthetic difference. Despite this purely aesthetic difference, for some reason, the PC fittings cost anywhere from 60% to 225% more for the consumer than than comparable SS ones. So at a current price of $7.50-$8.50 (though EK very recently lowered this price, and I used web page archiving like Wayback machine to see that they had previously been $9-$12) , it's crazy and aggravating to consider that EK (and other brands) are marking these fittings up anywhere from 340%-1700% above the price they paid for them, and all because the compression nut has knurling instead of wrench flats. This is why I have taken upon myself to challenge this pricing hegemony in this niche industry by "creating" my own fittings by simply using the body of an industrial compression fitting, removing the stock compression nuts, and instead using more aesthetically pleasing means of compression. In the end, the complete fitting costs me anywhere from just $2.50 to $5 depending materials and quality, and that without buying bulk. What's awesome is that I can drastically change the look of the fitting by swapping out the nut anytime I want, and I even quickly threw together a picture (included below) with four of the nuts I use the most, all of which are "off the shelf", meaning standard/typical/can be bought by anyone at anytime items. I'm currently trying to get my own business off the ground to sell these and some other innovative items I've created for PC modders/enthusiasts so hopefully that'll happen soon. Perhaps the my most promising creation is pre-sleeved wire for making custom PC cables/wiring harnesses. It's 16awg cable that comes with a braided sleeving made from a nylon derivative (way stronger as well as being UV and chemical resistant) that looks and feels like paracord. The sleeving is added on during the manufacturing process (which I personally created/innovated as a process that can be added onto any standard industrial braider) and is bonded directly to the wire's PVC jacketing. This means that the sleeving is always taught and can never slide, slip or move. Best of all, the labor required to create a custom extension is reduced, literally by, upwards of 80%-90%, in fact, without prior experience, you can create a 24 pin ATX harness in under an hour that looks perfect. This is because, to create the custom cables, all you have to do is cut your desired length and simply strip the ends, crimp your pins, and put them in the connector....no heatshrink, no lighters, no loose sleeving, no frayed sleeving....honestly, if I can get it to market, I think it'll completely gut the small time custom cable makers charging a fortune as well as the big time sleeving manufacturers. Why would anyone buy sleeving and go through the frustration and trouble when do don't have to. Best part, thanks to the authoritarian government, lax labor laws, safety regulations and highly exploited labor, I can theoretically sell this pre-sleeved wire to the customer at just a few pennies more per foot than the unsleeved wire alone. I've also included a picture of some of my preliminary samples below.
Do ask the editors to post a link your your shop when you are ready to sell.
Feel free to reach out to me by PM if you want to discuss EU distribution too.