Saturday, October 9th 2021
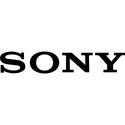
Sony and TSMC Said to be Planning US$7 Billion Chip Fab in Japan
There doesn't seem to be a single month where rumours about new TSMC plants around the world are popping up and this time around it looks like there might be a joint venture with Sony in Japan. According to the Nikkei, the Japanese government is likely to be involved and might foot as much as half of the US$7 billion bill.
Another much more unknown player, Japanese auto parts maker Denso is also said to be a potential participant in the new fab. Denso is said to supply Toyota among others and with a shift towards more EVs, this might not be such a strange move. The new fab is expected to be located in Kumamoto Prefecture on land owned by Sony. It should be noted that Sony already manufactures image sensors here and the factory was hit badly by a large earthquake back in 2016, which led to a global shortage of certain image sensors.If the joint venture goes ahead, this would be TSMC's first chip plant in Japan and also its first joint venture with Sony at this scale. The fab would, at least at the early stages, be focusing on image sensors, image processors and components for EVs, although as it'll take a couple of years at least to build the fab, this isn't set in stone. The Japanese government is said to be looking at getting a commitment from TSMC that chips made at the new fab will be prioritised for the Japanese market.
Source:
The Nikkei
Another much more unknown player, Japanese auto parts maker Denso is also said to be a potential participant in the new fab. Denso is said to supply Toyota among others and with a shift towards more EVs, this might not be such a strange move. The new fab is expected to be located in Kumamoto Prefecture on land owned by Sony. It should be noted that Sony already manufactures image sensors here and the factory was hit badly by a large earthquake back in 2016, which led to a global shortage of certain image sensors.If the joint venture goes ahead, this would be TSMC's first chip plant in Japan and also its first joint venture with Sony at this scale. The fab would, at least at the early stages, be focusing on image sensors, image processors and components for EVs, although as it'll take a couple of years at least to build the fab, this isn't set in stone. The Japanese government is said to be looking at getting a commitment from TSMC that chips made at the new fab will be prioritised for the Japanese market.
23 Comments on Sony and TSMC Said to be Planning US$7 Billion Chip Fab in Japan
so doesn’t ASML make the machines that etch/process the silicon wafers and fab buy the machines from them?
so why can’t any company buy a machine and start fabbing? Are the machines sold incomplete or is the final set up done by the end fab such as TSMC and that’s what is the secret sauce to getting a small nodes and good yields? Or is it more than that??
PS: time costs money.
Money aside, a lot of it comes down to expertise as well. Just look at how both Intel and GloFo struggled at one point. Intel obviously had more money to throw at the problem than GloFo, who gave up and stopped working on node shrinks, at least for the time being. On top of that, the machines from ASML are only part of the process.
Just as in any other industry, starting from scratch, even if you can use the same equipment and infrastructure, doesn't mean you'll make equal quality products. It's also a huge difference between screwing up in a sawmill and screwing up in a chip fab, as a dumb example, but I hope you get my point.
This is not a political who/what versus who/what thread.
This is a tech forum not your political soapbox.
The machines are not some kind of mass-produced stuff, either - you order one a couple years in advance, it's made to your specification, you help developing it, and it contains parts and know-how provided by you.
And all they do is projecting patterns on your wafers in UV light. Etching comes later. ASML scanners are just the most notorious because they are so complex and costly. There are other machines that also work close to the limits of physics, like those for vapor deposition, and I'm sure they're also complex and costly and hard to manage too.
Sony and Denso aren't going for all that as no one but TSMC/Samsung/Intel itself can afford that. Their goal is to make "image sensors, image processors and components for EVs", and something like 28 nm is going to be good enough for that.
2. etching machines are another beast and they are made by multiple diffrent companies you also have dry eych and wet etch.
3. on top of those machines you have testing machine of many types.
4. a normal fab can have up to 40 types of machines with the range of 30 to 80 of each one.
5. ASML can manufacture up to 50 a year at current.
6. Each one of those can run up to 170 new model (old model was 134 if i remember ) wafers per hour and like i said it a multi step process and iit can be anywhere form 100 steps up to 600.
7. Fabs like intel, TSMC, GF and others run from 5000 to 20000 wafers in the line.
8. From all of the above you can understand why you need multiple of those machines.
9. There is a wait list and even if you order now you'll probaly get the machine in 2025.
10. I'm not going to go into what it even takes to build a fab, develop your process, train personal to keep the line runing and do all of the maintenance on the different machine and not to forget the cost of chemical, gass, electricity, water, wages and etc.
11. Even a small fab can need an investment of up to 2 billion if you want the use EUV.
12. All of what i wrote is a super simplification.
One can't simply get a few billions out of their pocket (ironically, many people can) and build themselves a fab.
All this is why there are not many fabs that run EUV.
Just imagine if 5nm chips were so common that even your stove would use them. We'd probably be heavily augmented cyborgs waging space wars. Or most likely we'd be all dead. :D If anything, human kind has shown that they can't be trusted with high tech en masse. Inb4 mobile phones are more of a point in case than on the contrary.
This was before globalisation which had people forget this. Your money is as good as its origin. You have to be entrenched in the economy you are dealing with in order for it to have currency value.
Once you begin thinking this way, you figure there are no middle men in high tech.
So the machines themselves, in compare again to another analogy, is like buying a shortblock engine, you get the basic machine, then your staff/plant does the tweaking (heads, camshaft, carb/fuel injection) to get the results/node/output it desires (over simplification) but the gist of it?
So say an old 45nm node/machine/equipment, say if someone like TSMC itself is selling that off, and a smaller company like UMC buys it, then the tooling should be negligible?
So like everything in heavy industry its a big complex beast of a system, but also like heavy industry, pretty much all the items to build the plants are off the shelf so to speak, it's getting the expertise and capital to make it happen.
Sounds like cool place to get a tour.
This is why you can't easily transfer a design made for TSMC's nodes to say Samsung on a similar node. It's in fact often easier to start a new design for a specific fab node than to try and make an existing design work with a different foundry node.
The only time this sort of worked, was during the various fab node alliances, but even those required a lot of extra work if you want to move between foundries, as not everything was the same. How so? This isn't going to be a cutting edge fab, at least not based on what they're planning to manufacture there, if the Nikkei news post is anything to go by. Actually, you can't see much at all, since almost everything takes place inside the machines, due to the fact it has to be dust free.
Been to an Intel fab in Ireland and an NEC memory fab in Scotland and it was really quite boring. Never actually been invited to TSMC...
According to Wikipedia, a "normal" fab costs US$2-3 billion, but TSMC paid US$9.3 billion for at least one of its fabs and it's likely to cost even more in the future.
en.wikipedia.org/wiki/Semiconductor_fabrication_plant
patents............