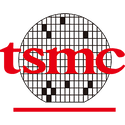
TSMC Prepares "CoPoS": Next-Gen 310 × 310 mm Packages
As demand for ever-growing AI compute power continues to rise and manufacturing advanced nodes becomes more difficult, packaging is undergoing its golden era of development. Today's advanced accelerators often rely on TSMC's CoWoS modules, which are built on wafer cuts measuring no more than 120 × 150 mm in size. In response to the need for more space, TSMC has unveiled plans for CoPoS, or "Chips on Panel on Substrate," which could expand substrate dimensions to 310 × 310 mm and beyond. By shifting from round wafers to rectangular panels, CoPoS offers more than five times the usable area. This extra surface makes it possible to integrate additional high-bandwidth memory stacks, multiple I/O chiplets and compute dies in a single package. It also brings panel-level packaging (PLP) to the fore. Unlike wafer-level packaging (WLP), PLP assembles components on large, rectangular panels, delivering higher throughput and lower cost per unit. Systems with PLP will be actually viable for production runs and allow faster iterations over WLP.
TSMC will establish a CoPoS pilot line in 2026 at its Visionchip subsidiary. In 2027, the pilot facility will focus on refining the process, to meet partner requirements by the end of the year. Mass production is projected to begin between the end of 2028 and early 2029 at TSMC's Chiayi AP7 campus. That site, chosen for its modern infrastructure and ample space, is also slated to host production of multi-chip modules and System-on-Wafer technologies. NVIDIA is expected to be the launch partner for CoPoS. The company plans to leverage the larger panel area to accommodate up to 12 HBM4 chips alongside several GPU chiplets, offering significant performance gains for AI workloads. At the same time, AMD and Broadcom will continue using TSMC's CoWoS-L and CoWoS-R variants for their high-end products. Beyond simply increasing size, CoPoS and PLP may work in tandem with other emerging advances, such as glass substrates and silicon photonics. If development proceeds as planned, the first CoPoS-enabled devices could reach the market by late 2029.
TSMC will establish a CoPoS pilot line in 2026 at its Visionchip subsidiary. In 2027, the pilot facility will focus on refining the process, to meet partner requirements by the end of the year. Mass production is projected to begin between the end of 2028 and early 2029 at TSMC's Chiayi AP7 campus. That site, chosen for its modern infrastructure and ample space, is also slated to host production of multi-chip modules and System-on-Wafer technologies. NVIDIA is expected to be the launch partner for CoPoS. The company plans to leverage the larger panel area to accommodate up to 12 HBM4 chips alongside several GPU chiplets, offering significant performance gains for AI workloads. At the same time, AMD and Broadcom will continue using TSMC's CoWoS-L and CoWoS-R variants for their high-end products. Beyond simply increasing size, CoPoS and PLP may work in tandem with other emerging advances, such as glass substrates and silicon photonics. If development proceeds as planned, the first CoPoS-enabled devices could reach the market by late 2029.